In the intricate world of industrial materials, choosing the right product is a crucial decision. It directly impacts the performance, durability, and cost-effectiveness of your projects. For companies operating in metal-dependent sectors like anti-corrosion coatings, chemicals, or metallurgy, Zinc Dust stands as an essential raw material. However, “zinc dust” isn’t a single, uniform product. It comes in various grades, each with distinct specifications, optimized for specific applications. Understanding these details is vital for buyers, engineers, and formulators to ensure they select the exact product that meets their project’s precise needs.
This comprehensive guide is specifically designed for industry professionals and procurement teams at trading companies like ATSOTEK. We’ll dive deep into the world of zinc dust grades, key technical specifications, and relevant industry standards. Our goal is to empower you with the knowledge needed to make informed decisions, streamline your procurement process, and guarantee the best possible performance for your industrial applications. By exploring the unique characteristics of each grade, we’ll help you discover the perfect zinc solution for your unique requirements.
Why Precise Zinc Dust Specifications Matter
Selecting the wrong zinc dust can lead to costly consequences, ranging from poor end-product performance to the rejection of entire material batches. Understanding the technical specifications of zinc dust isn’t just an academic exercise; it’s a practical necessity for ensuring quality and efficiency. These specifications define parameters that influence the chemical, physical, and electrochemical properties of the zinc, directly correlating with the success of the final application.
As a trading company, a thorough understanding of these details allows you to not only provide the right products to your clients but also to establish yourself as a trusted advisor in the industry. Your ability to precisely match a zinc grade to a client’s specific needs not only adds value but also strengthens long-term business relationships. This precision in raw material selection is what truly drives superior outcomes in industrial projects.
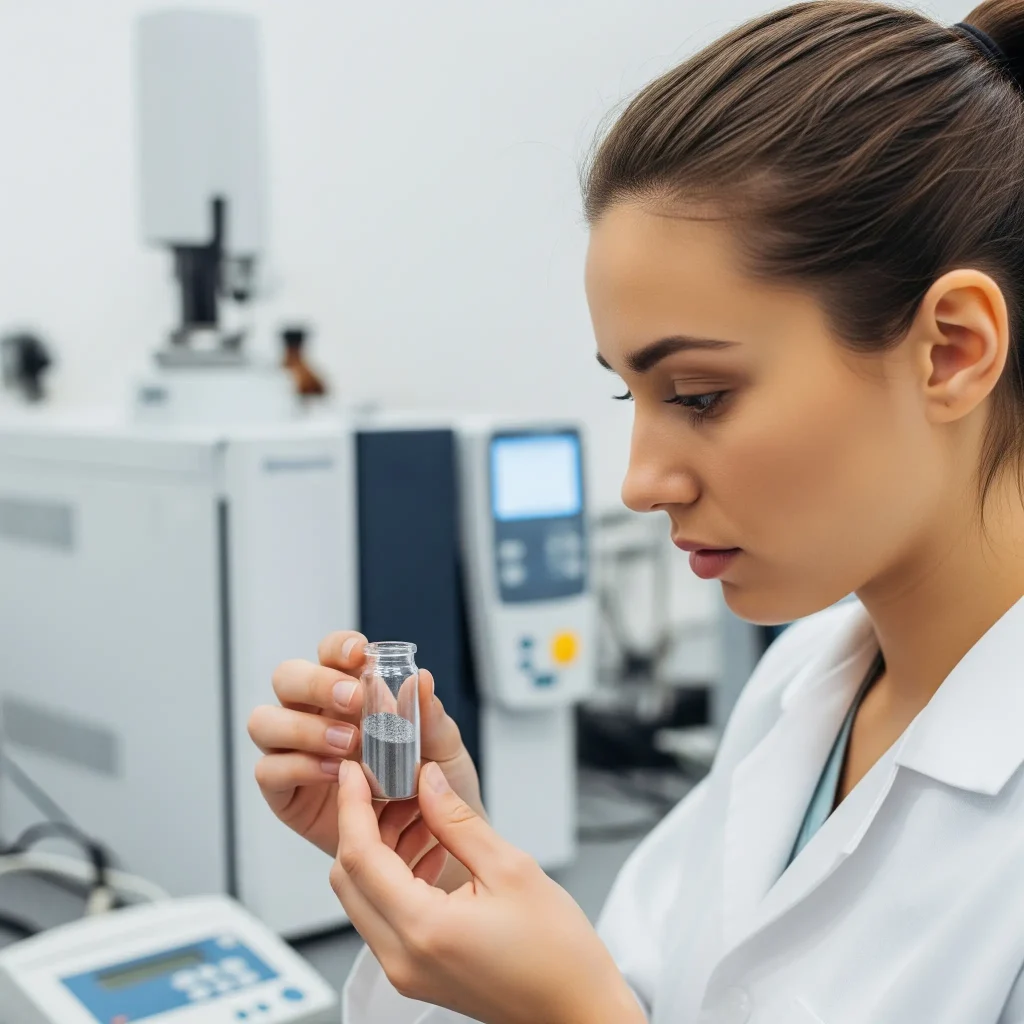
Key Physical Specifications of Zinc Dust
The physical properties of zinc dust, particularly those related to particle size and shape, significantly influence how it performs in various formulations and applications. These characteristics determine how zinc dust blends with other materials, how it packs into a coating matrix, and how effectively it covers a surface.
Engineers and chemists carefully evaluate these parameters when selecting the appropriate grade.To achieve optimal performance in the final product, you need a complete grasp of how these physical specifications impact the outcome. Each application might demand different physical properties, and choosing the grade that fulfills these needs is a fundamental step toward success.
Let’s explore the most important physical specifications:
Particle Size:
- Description: Typically expressed as the median diameter (D50) and particle size distribution (e.g., D10, D90). Different particle sizes are suitable for various applications.
- Importance:
- Anti-corrosion Coatings: Finer particles (typically 2 to 7 microns) offer a larger active surface area for galvanic protection and help create a smooth, uniform film. They also enhance the density and integrity of the protective barrier.
- Metallurgy: In certain metallurgical or reductive processes, specific particle sizes might be required for optimal reaction rates or the properties of the final product.
- Dispersion Stability: Finer particles disperse better in liquids (like paints), reducing settling.
Particle Shape:
- Description: Particles can be spherical, irregular, flaky, or dendritic (tree-like). The particle shape depends on the manufacturing method (e.g., atomization versus condensation).
- Importance:
- Coatings: Spherical particles contribute to better paint flow, while irregular particles might provide more inter-particle bonding in the dry film. Flaky particles are used in some coatings for barrier or reflective properties.
- Compaction: Particle shape affects how the powder compacts in processes like powder metallurgy.
Apparent Density / Bulk Density:
- Description: The weight of the powder in a given volume, usually in a loose or tamped state.
- Importance: Affects volume filling and the ease of powder handling and formulation. Higher apparent density means less air space in a formulation.
Specific Surface Area (SSA):
- Description: The total surface area of particles per unit of weight (typically square meters per gram). This property is inversely related to particle size; finer particles have a higher SSA.
- Importance: High surface area means higher reactivity, which is crucial in chemical and catalytic applications. It also impacts dispersion and adhesion in coatings.
Chemical Specifications and Purity: The Cornerstone of Performance
The chemical purity and elemental composition of zinc dust not only influence its performance in sensitive applications but can also define its specific grade and standard. Impurities, even in trace amounts, can sometimes disrupt the electrochemical performance of the zinc or trigger undesirable reactions in chemical processes.
Therefore, stringent control over the chemical composition is a critical aspect of producing and procuring high-quality zinc dust.For companies like ATSOTEK, acting as the bridge between manufacturer and consumer, ensuring chemical purity and adherence to client-required specifications builds trust and loyalty. Our clients seek the assurance that every batch of product they receive possesses the exact chemical characteristics promised.
Let’s explore the most important chemical specifications:
Zinc Purity:
- Description: The percentage of pure zinc (Zn) in the product. Typically expressed as 98.5%, 99%, or 99.5% Zn.
- Importance: For high-performance applications like advanced anti-corrosion coatings or the production of specific chemicals, higher zinc purity is crucial. Impurities can alter zinc’s electrochemical potential or cause unfavorable reactions.
Zinc Oxide Content (ZnO):
- Description: The percentage of zinc oxide present in the powder. This can be due to the manufacturing process or surface oxidation of zinc particles when exposed to air.
- Importance: Zinc oxide is not electrochemically active and cannot provide galvanic protection. High ZnO content can reduce anti-corrosion performance. In some applications, a small amount of ZnO is desirable for controlling zinc reactivity, but generally, its level should be controlled.
Impurities:
- Description: The presence of other elements such as lead (Pb), cadmium (Cd), iron (Fe), copper (Cu), tin (Sn), aluminum (Al), antimony (Sb), and chlorine (Cl). Each is measured in very small quantities (ppm).
- Importance:
- Lead and Cadmium: These elements are toxic and must be kept to a minimum in specific applications (like coatings for drinking water contact) or regions with strict environmental regulations.
- Iron and Copper: Can create unwanted galvanic cells within the powder or coating and alter the zinc’s electrochemical potential, potentially reducing protective efficiency.
- Chlorine: For certain chemical applications or coatings requiring resistance to chlorine, low chlorine levels are essential.
Moisture Content:
- Description: The percentage of water present in the powder.
- Importance: Moisture can lead to powder caking, undesirable reactivity, and reduced shelf life of the product.
Industry Standards and Certifications: Ensuring Global Quality
In the global trade of zinc dust, adhering to industry standards and holding valid certifications is absolutely vital for guaranteeing product quality and compliance with international requirements. These standards create a common language for manufacturers and buyers, setting benchmarks for quality, safety, and sustainability. For trading companies like ATSOTEK, the ability to supply products with these certifications significantly enhances credibility and customer trust.
Understanding these standards allows you not only to classify products correctly but also to assure your clients that the products they purchase from you have been manufactured through rigorous quality control processes and adhere to global benchmarks. This compliance, especially in export markets, is often a legal or commercial imperative.
The most important standards and certifications include:
ASTM (American Society for Testing and Materials):
- ASTM D520: A common American standard covering specifications and test methods for zinc dust used in paints and coatings. This standard specifically defines different grades (e.g., Type I, II, III) based on particle size, purity, and zinc oxide content.
ISO (International Organization for Standardization):
- ISO 3549: This international standard defines zinc powder for use in paints. It includes chemical and physical specifications that help ensure product quality and uniformity on a global scale.
MSDS (Material Safety Data Sheet) / SDS (Safety Data Sheet):
- Description: These documents provide crucial information on potential material hazards (health, safety, environmental) and how to handle, store, and transport them safely.
- Importance: Legally required in many countries for chemical products and essential for end-users and logistics companies. A comprehensive MSDS demonstrates a manufacturer’s commitment to safety and compliance.
REACH (Registration, Evaluation, Authorisation and Restriction of Chemicals):
- Description: A European Union regulation overseeing the registration, evaluation, authorization, and restriction of chemicals. It is mandatory for importing chemical substances into the European market.
- Importance: For trading companies looking to export zinc dust to European countries, REACH compliance is essential.
ROHS (Restriction of Hazardous Substances):
- Description: A directive in the European Union that restricts the use of certain hazardous materials in electrical and electronic equipment.
- Importance: While zinc dust is not directly used in electronics, its presence in related processes or other raw materials might require ROHS compliance checks.
Quality Management System Certifications (e.g., ISO 9001):
- Description: Indicates that the manufacturer has a robust quality management system in place to ensure product consistency and quality.
- Importance: Builds buyer confidence and demonstrates a commitment to standardized production processes.
Industrial Applications and Proper Grade Selection
The selection of the appropriate zinc dust grade directly depends on the final industrial application. Each industry, and even each specific process, has unique requirements regarding the physical and chemical properties of the zinc. Understanding these needs is the cornerstone of providing the best solutions for clients. Successful trading companies don’t just supply materials; they become valuable consultants in material selection.
As a supplier, you must not only know your product specifications but also understand your clients’ end-applications. This deep understanding enables you to offer the best recommendations and add significant value to the supply chain.
Here are some common applications and their related specifications:
Paint & Coatings Industry:
- Application: Manufacturing zinc-rich primers for corrosion protection of steel structures, ships, bridges, and infrastructure.
- Key Specifications:
- Particle Size: Fine and uniform (2-7 microns) for good adhesion and film uniformity.
- Zinc Purity: Very high (98.5% to 99.5% Zn) for maximum galvanic protection.
- Zinc Oxide Content: Low (less than 0.5%) to ensure maximum active zinc is available.
- Apparent Density: Suitable for dispersion and high loading in paint formulations.
Metallurgy & Reductive Processes:
- Application: In reductive processes (e.g., for gold and silver extraction from cyanide solutions – Cementation), production of other metal powders, or in powder metallurgy.
- Key Specifications:
- Zinc Purity: Very high, depending on the specific reductive process needs.
- Reactivity: High Specific Surface Area (SSA) for optimal reaction rates.
- Impurities: Very low levels of specific elements that might interfere with the reaction or reduce the purity of the final product.
Chemical Industry:
- Application: As a reducing agent in organic synthesis, production of sodium hydrosulfite, and other chemical processes.
- Key Specifications:
- Zinc Purity: Typically high, depending on reaction sensitivity.
- Reactivity: High (high SSA) for efficient reactions.
- Impurities: Strict control over impurities that might act as undesirable catalysts or contaminate the final product.
Battery Industry:
- Application: In the production of certain battery types (e.g., zinc-air batteries) as the anode.
- Key Specifications:
- Zinc Purity: Very high.
- Particle Size: Usually very fine (micron or even nano) for increased surface area and energy density.
- Impurities: Very low to prevent self-discharge or side reactions.
Certificates of Analysis (CoA) & Conformance (CoC): Transparency in Trade
To guarantee that zinc dust aligns with requested specifications, Certificates of Analysis (CoA) and Certificates of Conformance (CoC) are essential documents in international trade. These documents are issued by the manufacturer and detail the chemical composition, physical properties, and confirm compliance with agreed-upon standards or specifications.
Providing these certificates to clients enhances transparency and builds their trust.At ATSOTEK, we ensure that every batch of zinc dust we supply comes with a comprehensive CoA or CoC. This approach showcases our commitment to quality, accuracy, and accountability in every transaction we make. These documents are vital for quality assessment by your clients, as well as for customs and regulatory inspections.
Conclusion: Making Smart Choices for Lasting Performance with ATSOTEK
When selecting zinc dust for industrial applications, the details truly matter. From micron-sized particles to parts-per-million chemical purity, every specification impacts the success of your final project. A deep understanding of grades, physical and chemical properties, and industry standards forms the bedrock of smart decisions that ensure optimal performance and the longevity of your assets.As your trading partner, ATSOTEK is more than just a supplier of high-quality zinc dust; we are a reliable source of knowledge and expertise.
We help you navigate the complexities of zinc specifications and pinpoint the exact grade you need. With a commitment to quality, transparency, and unparalleled support, ATSOTEK delivers the best zinc dust solutions to empower your industrial operations and achieve superior corrosion protection. For expert consultation and to fulfill your needs, contact us today.