In the competitive world of industrial raw materials, quality isn’t a luxury; it’s an absolute necessity. Especially for products like Zinc Dust, which plays a vital role in critical applications such as corrosion protection, chemical processes, and metallurgy, any fluctuation in quality can have severe consequences. Poor performance, material waste, production downtime, and even safety hazards are just some of the problems stemming from inadequate quality control.
At ATSOTEK, we fully understand this. Our commitment to supplying Zinc Dust of the highest quality isn’t just a slogan; it’s deeply embedded in our rigorous quality control protocols.This blog gives you an in-depth look into our quality control process. We’ll show you how ATSOTEK ensures the precision and integrity of every Zinc Dust shipment, from sourcing to final delivery. Our goal is to not only inform you about the technical details but also to build your confidence in our capabilities as a reliable supplier of this crucial raw material for your industrial operations. By understanding these processes, you can confidently look to ATSOTEK as your trusted partner for Zinc Dust supply.
Why Zinc Dust Quality Control is Crucial
Zinc Dust is a versatile material, and its properties directly impact the final performance of your product or process. Its precise specifications, from particle size to chemical purity, can make the difference between a project’s success and failure. Imagine an anti-corrosion coating that loses its effectiveness due to low zinc purity, or a chemical reaction that fails to proceed correctly because of unwanted impurities.
These scenarios incur significant financial costs and can damage your operation’s reputation and safety.For ATSOTEK, quality control means protecting your investment. By adhering to the most stringent standards, we ensure that the products you receive possess the exact specifications necessary for your optimal results. This proactive approach reduces risks and adds lasting value to your supply chain.
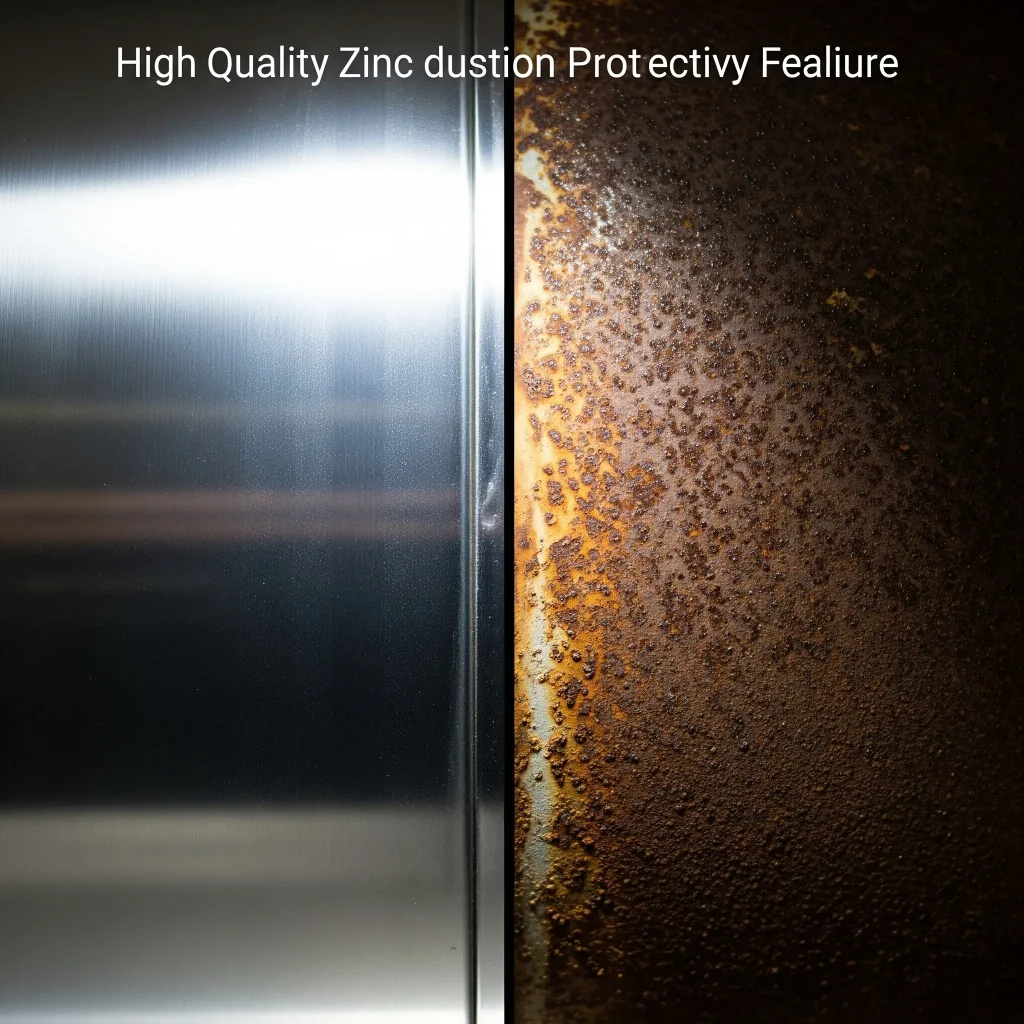
Sampling Protocols: The Starting Point of Precision
The cornerstone of any effective quality control process is accurate and representative sampling. Without a sample that truly reflects the entire product batch, any testing becomes invalid. At ATSOTEK, we deeply understand the importance of this initial step and have developed our sampling protocols based on industry standards and best practices.
These protocols ensure that every sample taken for analysis provides a true picture of the overall Zinc Dust batch quality.Our sampling process is meticulously executed to prevent cross-contamination and ensure samples are maintained in conditions that preserve their properties until testing. This precise first step forms the foundation for all subsequent tests and establishes the initial layer of quality assurance.
Physical Tests: Unveiling Structure and Properties
The physical properties of Zinc Dust significantly affect how it performs in various applications. These characteristics determine how the powder flows, disperses in a liquid, and forms a uniform coating.
ATSOTEK’s quality control team conducts a comprehensive set of physical tests to meticulously evaluate every Zinc Dust batch.These tests help us ensure that the product’s physical characteristics match your final application’s precise requirements, including ease of use, coverage, and durability.
The most important physical tests include:
Particle Size Distribution (PSD):
- This test determines the distribution of particle sizes within a sample. We typically provide D10, D50 (median size), and D90 values. D50 indicates the particle size at which 50% of the sample is smaller.
- Importance: For anti-corrosion coatings, the right particle size distribution is crucial for achieving a smooth, uniform film and maximizing the surface area for galvanic protection. In powder metallurgy, PSD influences compaction density and the mechanical properties of the final product.
Specific Surface Area (SSA) Determination:
- This test measures the total surface area of particles per unit of weight (typically square meters per gram). The BET (Brunauer, Emmett, Teller) method is a standard technique for this purpose.
- Importance: A high SSA indicates greater reactivity, which is vital in chemical applications (as a reducing agent) or catalytic processes. It also affects adsorption capacity and dispersion in coatings.
Apparent Density:
- This metric measures the weight of the powder in a given volume in a loose or tapped state.
- Importance: Apparent density impacts how the powder fills specific volumes and its ease of handling in manufacturing processes. In paint formulation, it affects zinc loading and paint consistency.
Particle Morphology:
- We use Scanning Electron Microscopy (SEM) for visual inspection of particle shape, surface characteristics, and any particle agglomeration.
- Importance: Particle shape (e.g., spherical, irregular, or flaky) can influence powder flowability, compaction behavior, and film formation in coatings.
Chemical Tests: Ensuring Purity and Performance
Beyond physical properties, the chemical composition of Zinc Dust is a defining factor in its efficacy and safety. Impurities, even in trace amounts, can significantly affect the electrochemical properties of zinc, reaction rates, or even the health of end-users.
ATSOTEK’s quality control laboratory employs advanced techniques to perform comprehensive chemical analyses on every batch of Zinc Dust.These tests ensure our product is not only pure but also free from any impurities that could compromise your final application or interfere with environmental and health regulations.
The most important chemical tests include:
- Zinc Purity Analysis:
- We determine the percentage of pure metallic zinc in the product using precise titration or spectroscopic methods.
- Importance: High purity is crucial for effective galvanic protection in anti-corrosion coatings and for zinc’s role as a reducing agent in chemical processes.
- Zinc Oxide (ZnO) Content Determination:
- This test measures the amount of zinc oxide (ZnO) present in the powder.
- Importance: Zinc oxide is not electrochemically active and cannot provide galvanic protection. Therefore, maintaining low ZnO levels is essential to ensure maximum active zinc is available for the final application.
- Impurities Analysis:
- We rigorously check for trace elements like lead (Pb), cadmium (Cd), iron (Fe), copper (Cu), and chlorine (Cl) using techniques such as Inductively Coupled Plasma – Optical Emission Spectrometry (ICP-OES) or Atomic Absorption Spectrometry (AAS).
- Importance: Some of these impurities are toxic (e.g., lead and cadmium), and their levels must be strictly controlled for safety and environmental compliance. Others (e.g., iron and copper) can affect zinc’s electrochemical potential, reducing its anti-corrosion efficiency.
- Moisture Content:
- The percentage of moisture present in the powder is precisely measured.
- Importance: High moisture can lead to powder caking, reduced flowability, and even undesirable reactions during storage or processing.
International Standards and Certifications: A Commitment to Global Compliance
In the global market, adherence to international standards is a benchmark for quality and reliability. ATSOTEK upholds this principle, ensuring that all Zinc Dust we supply complies with the most reputable industry standards. This compliance assures our clients worldwide that they receive products of consistent and reliable quality.For every shipment, we provide Certificates of Analysis (CoA) and Material Safety Data Sheets (MSDS/SDS).
These comprehensive documents cover all technical specifications, test results, and necessary safety information, providing complete transparency throughout the supply chain. Furthermore, we ensure our products comply with regional regulations like REACH and ROHS in export markets, where applicable.
The Role of Quality Control in ATSOTEK’s Supply Chain
At ATSOTEK, quality control isn’t just a final step; it’s an integral component of our entire supply process. We work closely with reputable global suppliers who adhere to our stringent quality benchmarks. From initial supplier audits to continuous monitoring of their manufacturing processes, we ensure that quality is embedded at every stage of our sourcing.
Our proactive approach to quality control minimizes quality-related risks throughout the supply chain. This means less downtime for you, more consistent quality in your final products, and ultimately, greater peace of mind for your business. Partnering with ATSOTEK means partnering with a company that values your quality as much as its own.
Conclusion: Choose ATSOTEK for Unwavering Assurance
In the world of industrial materials, when it comes to Zinc Dust, quality is paramount. ATSOTEK’s rigorous and comprehensive quality control process ensures that every batch of product you receive from us meets the highest standards. We provide you with a product that not only meets technical specifications but also enhances the performance, durability, and safety of your industrial applications.
By choosing ATSOTEK as your Zinc Dust supplier, you’re not just getting a product; you’re gaining a reliable partner committed to transparency, expertise, and unparalleled quality. Contact us today to ensure your operations are always supported by the best possible materials.